Welcome to our comprehensive guide on understanding the concrete thickness required for car parks in Auckland. Whether you’re planning a construction project, curious about local building practices, or simply wondering, “How thick is the concrete in a car park in Auckland?”, you’ve come to the right place. In this article, we’ll explore the factors that influence concrete thickness, including vehicle loads, soil conditions, and local regulations, to ensure your car park is built to last. From light vehicle spaces to heavy-duty commercial lots, knowing the right concrete thickness is crucial for durability, safety, and long-term cost efficiency. Let’s dive in and break down everything you need to know.
The concrete thickness for car parks in Auckland typically ranges between 100mm and 150mm. For light vehicle parking, a thickness of around 100mm is common, while commercial car parks designed to handle heavier loads often require concrete slabs of 150mm or more. Local factors such as soil conditions, expected traffic, and Auckland’s building regulations may also influence the final thickness.
Table of Contents
Why Concrete Thickness Matters In Car Parks
The Role of Concrete Thickness in Car Park Durability
When designing a car park, one of the most critical factors to consider is the thickness of the concrete. It directly influences the structure’s durability, safety, and long-term cost efficiency. In a place like Auckland, understanding how thick the concrete in a car park should be is crucial for balancing safety, cost, and longevity.
How Concrete Thickness Handles Vehicles, Weather, and Wear
Concrete thickness plays a vital role in determining a car park’s ability to withstand heavy loads, fluctuating weather conditions, and general wear over time. Car parks are subject to the weight of various types of vehicles—from lightweight sedans to heavy trucks—which put significant pressure on the surface. A thicker slab of concrete ensures that the car park can support these loads without cracking or deteriorating prematurely.
In addition to vehicle weight, car parks face challenges from environmental factors like rain, temperature fluctuations, and even Auckland’s coastal climate, which can lead to moisture-related damage if the concrete is not thick enough. A thicker concrete slab provides a stronger, more weather-resistant surface, helping to prevent cracks, erosion, and damage over time. This means fewer repairs and a longer lifespan for the car park.
Consequences of Using Too Thin or Too Thick Concrete
Using concrete that is too thin can lead to serious problems. Thin concrete slabs are more prone to cracking under the pressure of heavy vehicles, resulting in an unsafe surface and requiring expensive repairs. Over time, the cracks can worsen, compromising the structural integrity of the car park and making it less safe for vehicles and pedestrians.
On the other hand, using concrete that is too thick can result in unnecessary expenses. While a thicker slab may provide extra durability, it could be considered over-engineering if the additional thickness does not offer significant benefits relative to the cost. For instance, car parks designed to handle light vehicles don’t need excessively thick concrete. Overbuilding can significantly increase project costs without corresponding gains in safety or longevity.
Potential Costs of Repair Due to Incorrect Concrete Thickness
If the incorrect concrete thickness is used during construction, the long-term costs can be substantial. Repairs to a car park with insufficiently thick concrete may include filling in cracks, resurfacing, or even replacing sections entirely. These repairs are not only expensive but also disrupt car park usage, potentially leading to lost revenue if the facility has to be closed temporarily. Properly assessing the required thickness from the start ensures that these costly repairs are avoided.
Importance of Load-Bearing Capacity, Safety, and Longevity
The thickness of concrete in a car park is directly related to its load-bearing capacity, which is essential for ensuring the structure can support all types of vehicles safely. A well-constructed car park with the right concrete thickness provides greater safety for drivers and pedestrians alike, reducing the likelihood of accidents caused by structural failure. Additionally, the right thickness contributes to the longevity of the car park, minimizing the need for frequent repairs and extending the overall life of the structure.
Cost-Efficiency vs Over-Engineering
Achieving the perfect balance between cost-efficiency and durability is key when determining how thick the concrete in a car park should be. While thinner concrete may be cheaper upfront, the long-term repair costs can make it far less economical. On the other hand, opting for concrete that is too thick can lead to higher initial construction costs, offering little extra benefit in return.
In Auckland, where balancing these factors is crucial, understanding the importance of concrete thickness helps ensure that car parks are safe, durable, and cost-efficient for years to come.

Standard Concrete Thickness For Car Parks In Auckland
When designing car parks in Auckland, selecting the appropriate concrete thickness is essential to ensure durability and long-term performance. This decision directly affects the structure’s ability to withstand both light and heavy vehicle traffic. Understanding the standard guidelines for concrete thickness in New Zealand, particularly Auckland, helps in creating a car park that is both cost-effective and resilient.
General Guidelines for Concrete Thickness in New Zealand
In New Zealand, general guidelines for concrete thickness in car parks are designed to cater to different vehicle types and traffic volumes. For domestic and small business car parks, which primarily accommodate light vehicles, the recommended concrete thickness typically falls between 100mm and 120mm. This thickness ensures sufficient durability while minimizing the overall construction costs.
For heavy-duty car parks, such as those serving commercial buildings, shopping malls, and industrial zones, the required concrete thickness increases to handle the higher load demands. These car parks generally require concrete thickness ranging from 150mm to 200mm or even more, depending on specific traffic patterns and vehicle types.
Auckland-Specific Requirements for Car Park Construction
In Auckland, where urbanization and high traffic density are common, ensuring the right concrete thickness is crucial for long-lasting car parks. Auckland’s specific conditions, including weather patterns and soil types, influence the decision-making process for car park construction. While the general New Zealand guidelines apply, Auckland developers may consider additional reinforcement methods, such as steel rebar or mesh, to enhance the concrete’s strength, particularly in areas with higher rainfall or heavy traffic.
Moreover, compliance with the Auckland Council’s building codes is essential when designing and constructing car parks. These codes may stipulate particular requirements for drainage, surface treatments, and load-bearing capacity, all of which can impact the choice of concrete thickness.
Light Vehicle Car Parks
For car parks that cater primarily to light vehicles, such as domestic driveways or small business parking lots, a concrete thickness of 100mm is generally sufficient. This is the industry standard in Auckland and across New Zealand, ensuring that the car park can easily handle regular vehicle traffic without premature wear and tear.
Heavy Vehicle Car Parks
Car parks intended for heavy vehicles, such as delivery trucks, buses, or commercial fleets, demand significantly thicker concrete. In Auckland, it is common for these heavy-duty car parks to have concrete thickness starting from 150mm and potentially exceeding 200mm in areas where the vehicle load is particularly intense. These thicker slabs are often reinforced with steel or mesh to increase their load-bearing capacity and prevent cracking under heavy loads.
Comparison to International Standards
When compared to international standards, Auckland’s concrete thickness recommendations align closely with global norms. For example, in countries like the United States, the standard concrete thickness for light vehicles is around 100mm to 125mm, similar to New Zealand’s standards. For heavy vehicles, international standards suggest concrete thicknesses of 150mm to 200mm or more, which is also consistent with Auckland’s industry practices.
In Auckland, typical concrete thickness for car parks ranges between 100mm for light vehicles and up to 150mm or more for heavy commercial usage. These guidelines, based on both local and international standards, ensure the construction of durable, long-lasting car parks that can withstand various vehicle loads. Whether building a residential driveway or a large commercial parking facility, adhering to these concrete thickness recommendations is essential for a robust, sustainable structure.
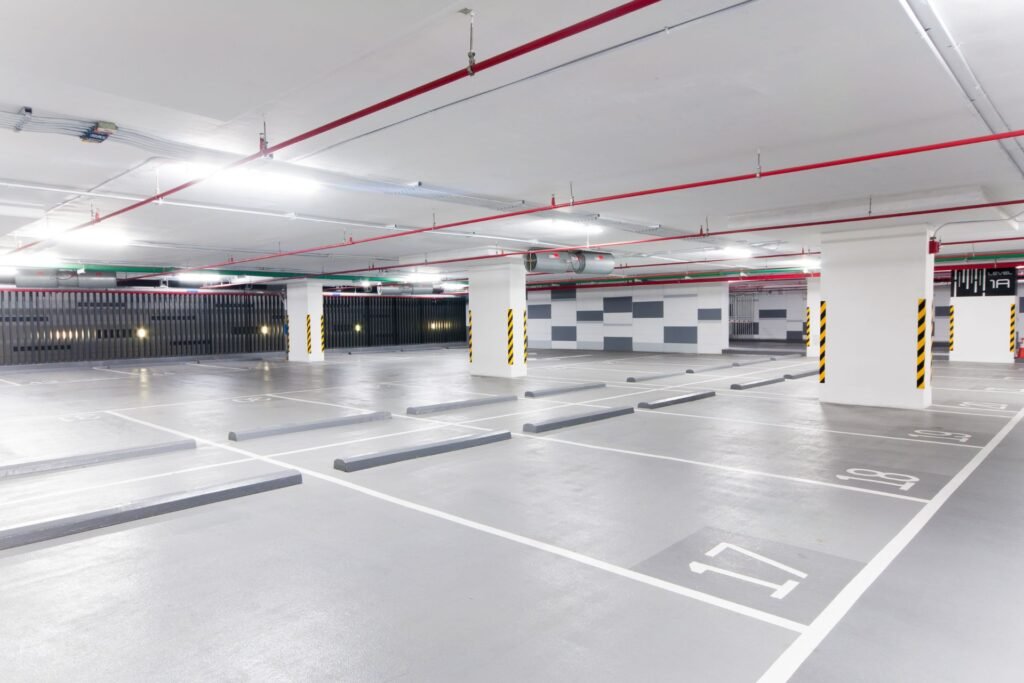
Factors That Influence Concrete Thickness In Auckland Car Parks
When it comes to building durable car parks in Auckland, one of the most critical aspects to consider is the concrete thickness. The right thickness ensures longevity, safety, and the ability to withstand the weight and movement of vehicles over time. But what determines the correct concrete thickness for a car park in this unique region? Several factors come into play, each affecting the structural integrity and overall performance of the concrete surface.
What Determines the Right Concrete Thickness?
There isn’t a one-size-fits-all answer when it comes to concrete thickness for car parks in Auckland. Several variables need to be considered, including the expected vehicle load, the underlying soil conditions, and the local climate. These elements significantly influence the design and ultimately, the thickness of the concrete slab required for optimal performance.
1. Vehicle Load
One of the primary factors that dictates concrete thickness is the type and number of vehicles that will regularly use the car park. Heavier vehicles, such as trucks and commercial vans, exert more pressure on the concrete than standard passenger cars. If the car park will accommodate heavy-duty vehicles or consistent traffic, the concrete will need to be significantly thicker to prevent cracking and wear over time. In contrast, car parks with lighter traffic or just personal vehicles may not require such a heavy-duty solution.
2. Soil Conditions
Auckland is known for its varied geological landscape, including volcanic soils and coastal areas. These differences in soil composition can have a substantial impact on how thick the concrete needs to be. Volcanic soils tend to be more stable, potentially requiring less concrete thickness compared to areas with looser, coastal soils. In regions where the ground is softer or more prone to shifting, a thicker concrete slab is necessary to ensure that the surface remains level and intact under pressure.
3. Local Climate
Auckland’s climate plays a crucial role in determining the appropriate concrete thickness for car parks. The city experiences heavy rainfall, particularly during the winter months, which can lead to water pooling and erosion if the drainage system and concrete surface aren’t designed properly. Moreover, the potential for earthquakes in Auckland adds an additional layer of consideration. A thicker concrete slab can provide more resilience to the seismic activity that occasionally affects the region, helping to reduce the risk of cracking or other forms of damage.
Key Points to Consider
When determining how thick the concrete in a car park in Auckland should be, factors such as vehicle weight, soil conditions, and weather come into play. Understanding these influences can help ensure that the concrete provides long-term durability, stability, and safety.
- Vehicle Traffic and Expected Loads: Car parks that accommodate heavier or more frequent vehicle traffic will require thicker concrete to prevent structural issues.
- Ground and Soil Stability: The stability of the soil beneath the car park is essential in determining how much support the concrete needs. Coastal and volcanic soils in Auckland require specific considerations.
- Drainage and Water Resistance: Adequate thickness, combined with a well-designed drainage system, can help protect the concrete from Auckland’s wet winters and prevent water from seeping through and damaging the base layers.
By addressing these factors during the planning and construction phases, car park developers can ensure that their structures meet Auckland’s unique environmental and geological demands, offering safe and long-lasting parking solutions for all types of vehicles.
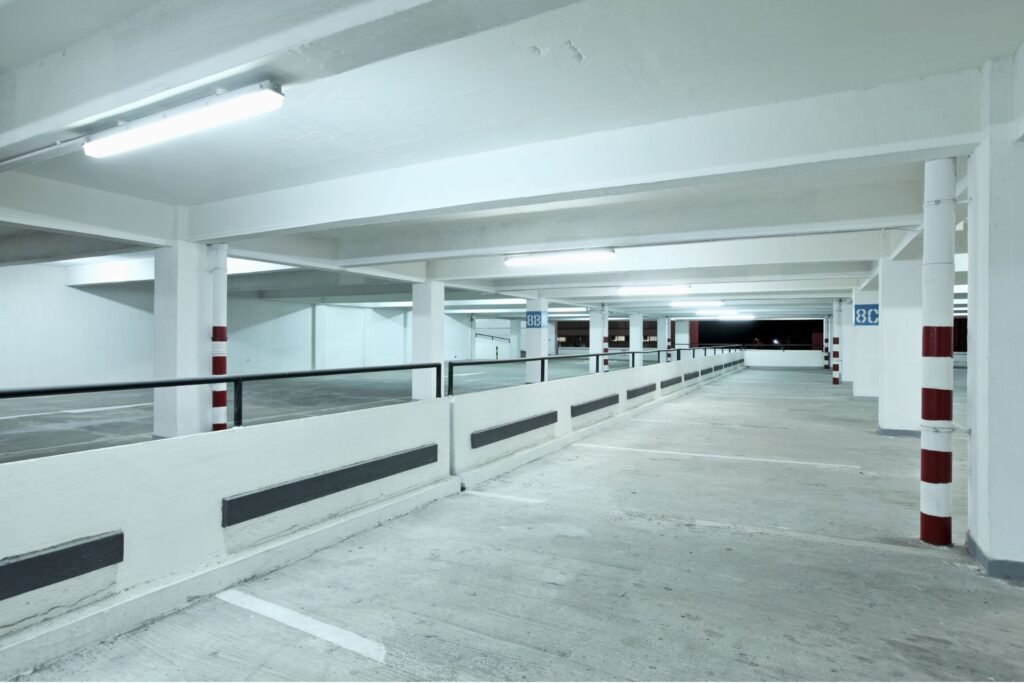
The Role Of Reinforcement In Concrete Thickness
When it comes to building durable and long-lasting car parks, the thickness of the concrete slab plays a crucial role. However, it’s not just about how thick the concrete is; reinforcement materials, such as steel rebar, mesh, or fiber-reinforced concrete, significantly impact the required thickness. This is especially important for car parks in Auckland, where the design must withstand constant vehicle traffic and wear.
Reinforcement Materials and Their Effect on Concrete Thickness
In construction, reinforcement materials are used to enhance the structural integrity of concrete. Without reinforcement, concrete is strong in compression but weak in tension, meaning it could crack or fail under stress. Steel reinforcement, such as rebar or mesh, helps prevent these failures, allowing engineers to reduce the overall thickness of the concrete slab while still maintaining the necessary strength.
Steel Reinforcement: Rebar and Mesh
Rebar (reinforcing bar) and mesh are the most commonly used reinforcement materials in concrete construction. Rebar consists of steel rods that are strategically placed within the concrete to resist tensile forces and prevent cracking. This allows for a thinner slab of concrete to be used while still supporting heavy loads, which is a common requirement in Auckland’s commercial car parks. Mesh, on the other hand, is a grid of steel wires that also reinforces the concrete but is typically used in less demanding applications or in combination with rebar.
Both rebar and mesh offer cost-effective solutions, particularly when working with larger projects or areas that experience significant traffic. For example, in high-traffic Auckland car parks, where the concrete will be subjected to heavy vehicles on a daily basis, steel reinforcement is crucial. The use of rebar or mesh in these settings not only ensures longevity but also helps reduce maintenance costs in the long run.
Fiber-Reinforced Concrete as an Alternative
An increasingly popular alternative to traditional steel reinforcement is fiber-reinforced concrete (FRC). This material contains small fibers—made from steel, glass, or synthetic materials—distributed throughout the concrete mix. The fibers work to increase the tensile strength of the concrete, making it more resistant to cracking and reducing the need for additional reinforcement materials like rebar.
Fiber-reinforced concrete offers several benefits, especially in areas where using traditional reinforcement methods might be challenging or too costly. In Auckland, FRC is particularly useful in smaller car parks or low-traffic areas where the demands on the concrete are not as extreme. Additionally, fiber-reinforced concrete can help lower labor costs since it simplifies the construction process by reducing the need for placing rebar or mesh.
When is Reinforcement Necessary in Auckland Car Parks?
The need for reinforcement in Auckland car parks largely depends on factors such as the expected traffic load and the type of vehicles that will use the space. For high-traffic or commercial car parks, steel reinforcement is often necessary to ensure that the concrete can handle the stress from constant vehicle movement. Reinforcement plays a key role in how thick the concrete in a car park in Auckland needs to be, especially in high-traffic or commercial areas. Without reinforcement, thicker slabs of concrete would be required, which increases both material and construction costs.
In lower-traffic areas or residential car parks, fiber-reinforced concrete can be a more economical option. It provides the necessary strength without the added expense of traditional reinforcement materials. This makes it a practical choice for projects that need to balance cost with performance.
Cost Considerations for Reinforcement
While using reinforcement materials like rebar, mesh, or fibers can increase upfront construction costs, the long-term benefits often outweigh these expenses. Reinforced concrete tends to have a longer lifespan, reducing the need for repairs and maintenance over time. In Auckland, where weather conditions and heavy use can lead to rapid wear and tear on car park surfaces, investing in reinforced concrete can save both time and money in the long run.
In summary, choosing the right type of reinforcement for concrete in car parks is a critical decision. Whether opting for traditional steel rebar or mesh, or more modern solutions like fiber-reinforced concrete, the proper use of these materials can reduce the required concrete thickness while still delivering a durable and cost-effective solution. When constructing car parks in Auckland, where traffic loads and environmental factors play a significant role, reinforcement is key to ensuring both structural integrity and long-term performance.

Case Study: Concrete Thickness In Auckland’s Major Car Parks
In this section, we’ll explore real-life examples of concrete thickness specifications in some of Auckland’s most prominent car parks. We’ll examine how these structures are designed to accommodate high traffic volumes and heavy loads, ensuring long-term durability while adapting to Auckland’s unique weather conditions and geological factors. Let’s dive into the specifics and learn about the innovations and lessons that have emerged from these projects.
Real-Life Examples of Concrete Thickness in Auckland’s Car Parks
Many large commercial car parks in Auckland, especially those located in shopping malls, office buildings, and other high-traffic areas, are constructed with thick, durable concrete slabs. For instance, some of the most notable car parks, like those at Sylvia Park, Westfield Newmarket, and the Auckland International Airport, are built with concrete slabs that measure 150mm or more in thickness. This thickness is crucial to managing the significant weight and wear from the continuous flow of vehicles, including heavy-duty vehicles like delivery trucks, buses, and SUVs.
Concrete thickness is a critical factor in these car parks, as it directly impacts the structure’s ability to resist cracking, subsidence, and general wear and tear. The thicker the concrete, the more it can distribute the pressure from the vehicle loads, ensuring that the car park remains functional for decades without significant repairs or maintenance.
Designing Car Parks to Withstand High Traffic and Heavy Loads
The car parks in Auckland’s busiest areas are not only built for volume but also to accommodate the increased pressure exerted by larger and heavier vehicles. Concrete thickness plays a vital role in ensuring these structures remain durable despite the intense daily use. For instance, commercial car parks, such as those in major shopping malls or office complexes, often experience hundreds or even thousands of vehicle entries and exits per day. This heavy load requires car park designs that include high-strength concrete, reinforcement through steel bars or mesh, and a thickness specification that is suited to the demands of the location.
Many large commercial car parks in Auckland use concrete with a thickness of 150mm or more to handle heavy vehicle loads and prevent cracking. This is especially important in high-traffic environments where the risk of surface deterioration is higher due to frequent braking, turning, and weight distribution.
Lessons Learned and Innovations in Auckland Car Park Design
Over the years, car park designers in Auckland have learned valuable lessons, particularly concerning how concrete thickness interacts with the city’s climate and ground conditions. Auckland’s geology includes soft soil in many areas, which can lead to issues like settling or cracking in car park surfaces if the concrete is too thin or improperly reinforced. Additionally, Auckland’s humid, rainy weather can cause water to seep into the concrete, leading to deterioration over time if proper precautions are not taken.
To combat these challenges, engineers have implemented several innovative solutions. One such innovation is the use of advanced waterproofing membranes beneath the concrete, preventing water ingress and extending the lifespan of the car park surface. Another technique is the integration of fibers into the concrete mix, adding extra strength to the slabs without significantly increasing their weight or cost. These fibers can help distribute stresses more evenly across the concrete, reducing the risk of cracking even in areas of high traffic.
Designers also consider Auckland’s seismic activity when determining concrete thickness. In an earthquake-prone region, car parks must be built with enough flexibility to withstand ground movement without suffering structural damage. This has led to the adoption of seismic-resistant designs that incorporate thicker concrete slabs and flexible joints, allowing for movement during an earthquake while preventing large-scale cracking or collapse.
Handling Auckland’s Weather and Geology in Car Park Design
Auckland’s weather and geological conditions require careful consideration when designing and constructing car parks. The city’s climate is characterized by frequent rain and humidity, both of which can degrade concrete over time if not properly addressed. By using thicker concrete slabs (150mm or more), coupled with advanced waterproofing solutions, designers can protect these surfaces from moisture damage, prolonging their lifespan.
Moreover, Auckland’s underlying soil can vary in stability, and this must be factored into the design of car parks. In areas where the ground is softer or more prone to shifting, thicker concrete slabs help distribute vehicle loads more effectively, minimizing the risk of cracks or subsidence. Engineers also reinforce these slabs with steel rebar or mesh to provide additional strength, ensuring the car parks remain stable even in challenging geological conditions.
In Auckland, car park design is a sophisticated process that involves careful planning, especially when it comes to the thickness of the concrete slabs. Many large commercial car parks in Auckland use concrete with a thickness of 150mm or more to handle heavy vehicle loads and prevent cracking. These design decisions ensure that Auckland’s car parks can withstand the pressures of heavy traffic, adapt to the city’s weather, and remain functional for years without major maintenance. Lessons learned from past projects and the adoption of innovative techniques have further enhanced the durability and safety of car parks across the city.
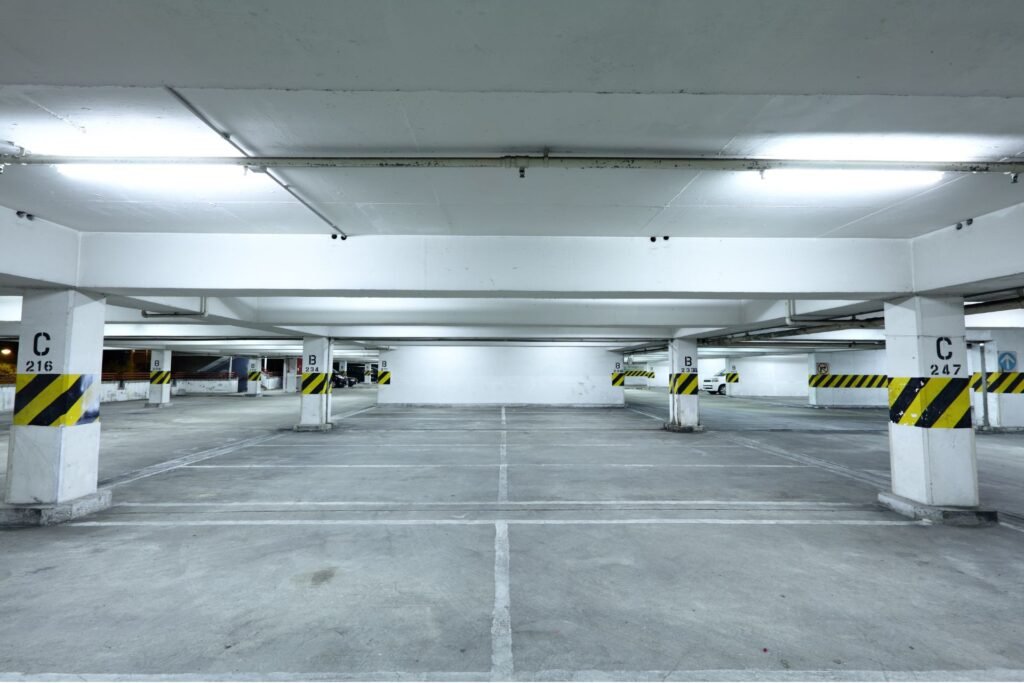
Local Building Regulations In Auckland For Car Park Construction
When it comes to constructing car parks in Auckland, understanding the local building regulations is essential. These regulations are designed to ensure that the construction is not only safe and sustainable but also compliant with the standards set by the city council. If you’re planning to build a car park in Auckland, knowing the ins and outs of these rules can save time, money, and avoid potential legal issues down the road.
Understanding Auckland’s Building Codes and Standards for Car Parks
Building a car park in Auckland is governed by specific building codes and standards that apply directly to this type of construction. The Auckland Council Building Code plays a significant role in shaping these requirements, particularly when it comes to structural integrity, drainage, environmental impact, and safety.
For instance, concrete thickness is a critical element when designing a car park. In Auckland, the local building regulations dictate how thick the concrete in a car park must be to ensure it meets both safety and environmental standards. The Auckland Council requires that concrete thickness be sufficient to handle the load of vehicles, resist wear over time, and accommodate any drainage systems necessary for stormwater management. Thicker concrete slabs are essential to prevent cracking, ensuring longevity, and minimizing the need for frequent repairs.
The Role of Resource Consents and Council Guidelines
Another important aspect of car park construction in Auckland is resource consents. These are necessary for many building projects, including car parks, particularly when the project may impact the environment or local infrastructure. The Auckland Council often requires resource consents to ensure that the proposed construction aligns with the city’s broader urban planning goals. This could include aspects like the car park’s size, drainage systems, environmental sustainability, and even the impact on traffic flow in the area.
Before any construction begins, it’s important to submit a detailed plan to the council, ensuring compliance with these guidelines. Failure to obtain the necessary resource consents or meet council regulations can lead to fines, construction delays, or even the demolition of non-compliant structures.
How Local Building Regulations Influence Concrete Thickness
One of the key factors in constructing a car park is determining the right concrete thickness, which is heavily influenced by local building regulations. The thickness is not just a matter of structural integrity, but also of environmental sustainability and safety. Auckland’s regulations specify that concrete must be thick enough to support the weight of vehicles, minimize cracking, and withstand the local climate, including Auckland’s frequent rainfall, which can affect the stability of the ground beneath a car park.
These regulations also ensure that drainage systems are incorporated effectively. Poor drainage can lead to water pooling, which not only damages the concrete but also poses safety hazards. Therefore, ensuring the right balance between thickness and drainage efficiency is crucial. The Auckland Council Building Code provides detailed specifications that guide engineers and builders in making these decisions.
In Auckland, adhering to local building regulations is not just a legal requirement—it’s a crucial step in ensuring the durability, safety, and environmental sustainability of car park construction. From understanding the necessary concrete thickness to securing resource consents, every detail must align with the standards set by the Auckland Council. By following these guidelines, builders can ensure that their car parks are not only compliant but also built to last.
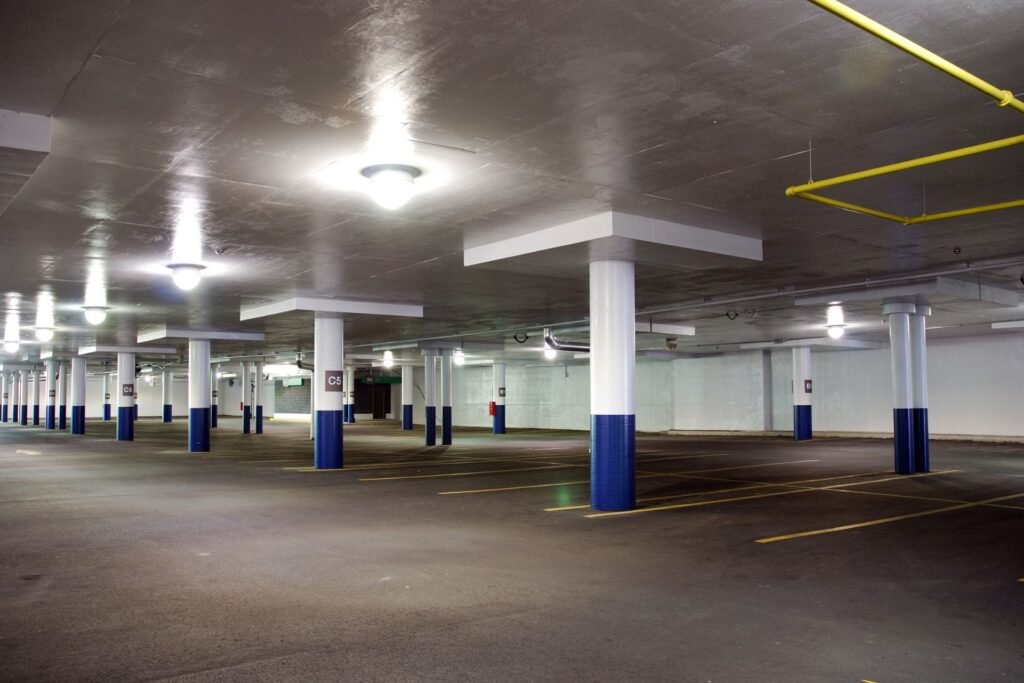
Costs And Considerations For Concrete Thickness In Car Parks
How Does Concrete Thickness Affect Car Park Construction Costs?
When planning a car park in Auckland, one of the most critical factors to consider is the thickness of the concrete. This decision plays a significant role in the overall construction costs and long-term expenses. Concrete thickness directly influences not just the upfront costs but also the durability and maintenance required over time.
Breaking Down the Cost Implications of Thicker vs Thinner Concrete
The cost implications of choosing thicker concrete over thinner alternatives are multifaceted. On one hand, thicker concrete requires more raw material, which increases the initial material costs. Additionally, labor expenses tend to rise due to the extended time required to pour, level, and cure thicker slabs. However, thinner concrete, while cheaper upfront, may lead to higher maintenance costs down the line, especially if it doesn’t provide adequate structural support for heavy vehicle traffic or weather conditions common in Auckland.
It’s essential to strike a balance between initial investment and future expenses. While a thicker slab may seem more expensive at the start, it can result in significant long-term savings due to its increased durability and reduced need for repairs. For example, a thinner concrete slab might develop cracks or require resurfacing more frequently, leading to recurring maintenance costs.
Initial Investment vs Long-Term Maintenance Savings
While the initial cost of installing thicker concrete is higher, it can offer substantial savings in the long run. A thicker slab is less prone to cracking, chipping, or other common wear-and-tear issues. This results in fewer repairs, lower maintenance costs, and extended longevity of the car park surface. In Auckland, where car parks often endure a wide range of weather conditions, including heavy rains and occasional temperature fluctuations, thicker concrete provides better resistance to these environmental factors.
Moreover, thicker concrete can handle heavier loads, which is especially beneficial for car parks that accommodate frequent commercial vehicle traffic. This reduces the risk of damage that could lead to costly repairs or even the need for a full resurfacing.
Impact on Overall Car Park Design Budget in Auckland
The design budget for a car park in Auckland will also be influenced by the chosen concrete thickness. Thicker concrete may lead to higher upfront material and labor costs, but this is offset by the reduced need for frequent repairs and lower long-term maintenance expenses. Car park designers and contractors in Auckland must weigh the benefits of investing in the right thickness against the overall project budget.
Additionally, reinforcement is another cost factor that ties into concrete thickness. Thicker slabs typically require more reinforcement, such as steel bars or mesh, to ensure they maintain their structural integrity over time. While this adds to the initial construction cost, it again reduces the likelihood of significant maintenance or repair needs, contributing to long-term cost savings.
In summary, while thinner concrete might appear to save money in the short term, investing in thicker, more durable slabs can lead to considerable financial benefits over time. When planning a car park in Auckland, it’s essential to consider how thick the concrete should be to avoid higher maintenance costs later on. Balancing the initial costs with future savings ensures a more cost-effective and durable parking solution.
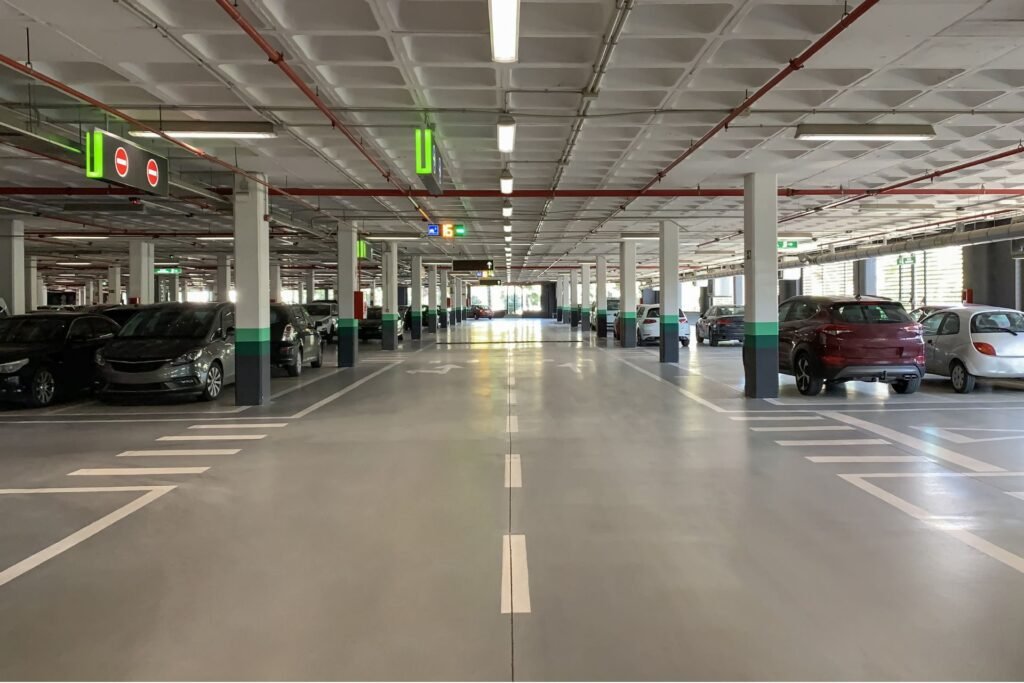
FAQs: About How Thick Is The Concrete In A Car Park In Auckland
How thick should the concrete be for a standard car park in Auckland?
The concrete thickness for a standard car park in Auckland is generally around 100mm to 150mm, depending on the type of vehicles expected to use it. Light vehicle parks typically use 100mm, while commercial car parks with heavy vehicles often require thicker slabs of 150mm or more.
What factors determine the concrete thickness in a car park?
Several factors determine the concrete thickness in a car park, including the weight and type of vehicles that will use the space, local soil conditions, climate considerations like rainfall and earthquakes, and Auckland’s specific building regulations.
Does the type of vehicle affect the required concrete thickness?
Yes, the type of vehicle significantly affects concrete thickness. For car parks used by light vehicles, such as cars and small trucks, a 100mm thickness is usually sufficient. However, for heavy vehicles like buses or delivery trucks, the thickness should be at least 150mm to withstand the additional load.
Is reinforcement necessary for all car parks?
While not always required, reinforcement is highly recommended for most car parks, especially those with high traffic or heavy vehicles. Reinforcement, such as rebar or mesh, helps strengthen the concrete, allowing it to withstand heavier loads and resist cracking over time.
Are there Auckland-specific regulations for car park concrete thickness?
Yes, Auckland has local building codes and regulations that may influence the required concrete thickness for car parks. These regulations ensure that car parks are built to safely handle expected loads, resist environmental factors, and comply with safety standards.
How does Auckland’s climate affect concrete thickness in car parks?
Auckland’s rainy climate, coupled with the possibility of seismic activity, can affect the durability of concrete. Thicker concrete, along with proper drainage systems and reinforcement, helps prevent cracking and water damage in areas that experience heavy rainfall.
What are the costs associated with thicker concrete in car parks?
Thicker concrete comes with higher material and labor costs, but it often results in long-term savings by reducing the need for repairs and maintenance. The initial investment in thicker concrete and reinforcement is generally worth it, especially in high-traffic areas or commercial settings.
Can thinner concrete slabs be used if the car park is only for light vehicles?
Yes, thinner slabs of around 100mm can be used for car parks designated for light vehicles, such as cars and small trucks. However, reinforcement is still advisable to enhance the durability of the slab and prevent cracks from developing over time.
How often should car park concrete be maintained or inspected?
Car parks should be regularly inspected, at least annually, to check for cracks, water damage, or wear and tear. Proper maintenance, such as sealing and repairs when necessary, can significantly extend the life of the concrete and reduce the need for expensive overhauls.
What happens if the concrete is too thin for the car park’s intended use?
If the concrete is too thin, it can crack, warp, or deteriorate quickly under the weight of vehicles. This may lead to costly repairs and could potentially create safety hazards. Using the proper concrete thickness for the expected load is essential to avoid these issues.
Conclusion
Understanding how thick the concrete in a car park in Auckland should be is key to ensuring safety, durability, and compliance with local standards. Selecting the correct thickness is crucial not only for meeting regulatory requirements but also for ensuring the longevity of your car park, especially with heavy traffic and wear over time. Adhering to Auckland-specific regulations and considering the long-term usage of the car park will help avoid costly repairs or safety issues down the line. To make the best decision, it’s highly recommended to consult with local experts or engineers who can provide tailored advice based on your specific needs. If you’re looking for more information or a personalized consultation, explore our site further to find expert guidance and resources.
About the Author:
Mike Veail is a recognized digital marketing expert with over 6 years of experience in helping tradespeople and small businesses thrive online. A former quantity surveyor, Mike combines deep industry knowledge with hands-on expertise in SEO and Google Ads. His marketing strategies are tailored to the specific needs of the trades sector, helping businesses increase visibility and generate more leads through proven, ethical methods.
Mike has successfully partnered with numerous companies, establishing a track record of delivering measurable results. His work has been featured across various platforms that showcase his expertise in lead generation and online marketing for the trades sector.
Learn more about Mike's experience and services at https://theleadguy.online or follow him on social media: